※ 毎朝、5分以内で読める書籍の紹介記事を公開します。
※そのままの文章ではありませんが、試し読みする感覚でお楽しみください。
目次
書籍情報
現場の「困った!」を解消する
基礎からわかる物流現場改善
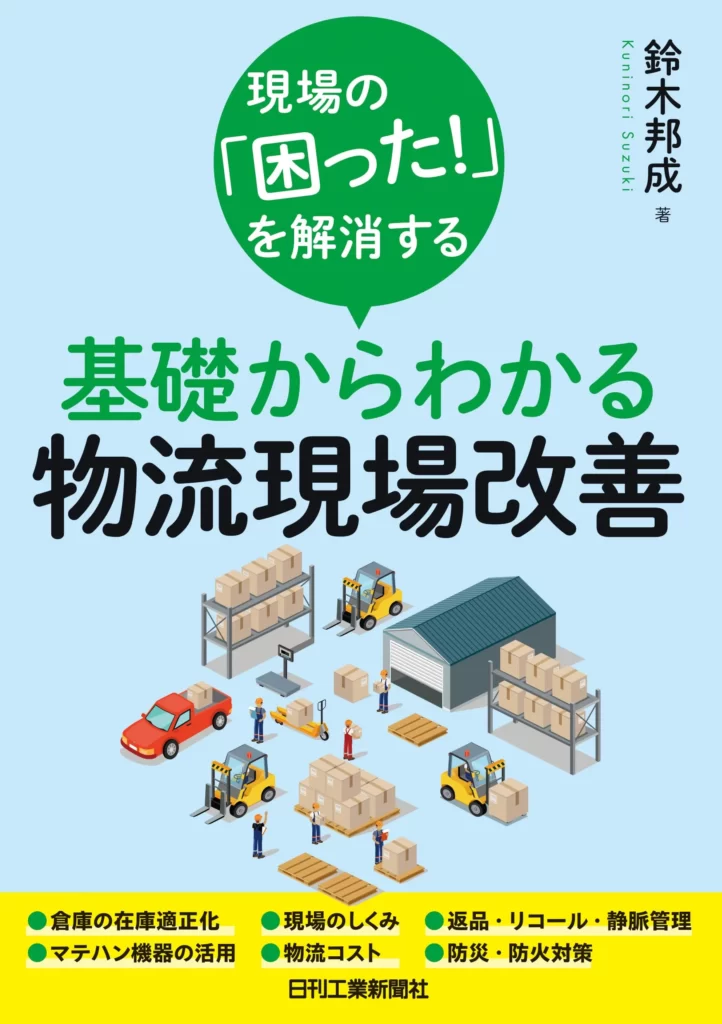
発刊 2023年8月30日
ISBN 978-4-526-08287-0
総ページ数 182p
鈴木邦成
物流エコノミスト、日本大学教授。レンタルパレット大手のユーピーアールの社外監査役も努めます。
日刊工業新聞社
- はじめに
- 第1章 物流現場での改善と現状分析
- 物流現場改善の考え方と方針
- 現場改善のセオリー
- 整理整頓により「見える化された倉庫」の魅力
- 荷姿を意識しながら作業効率を改善
- 「自動化」や作業工程数の削減で手荷役を減らす
- ムダを減らして物流コスト高騰に田泓
- 現場の課題を数値化して現状と原因を分析
- column 輸配送コストの削減
- 第2章 納期遵守と倉庫整理 納期遵守を重視しすぎて過剰在庫を誘発
- 納期遵守と適正在庫のギャップを解消したい
- この状況どうする 在庫が多く、保管スペースが不足している
- こうすれば改善できる 納期管理によって安全在庫の見える化を徹底し、庫内在庫の総量を抑える!
- 改善のコツ 納期管理シートで安全在庫を見える化
- 欠品の多発を解消したい
- この状況どうする 出荷部品が在庫切れとなっている
- こうすれば改善できる 出荷時期の迫る部品の保管スペースには、欠品の注意喚起の「赤札(赤紙)」を用意する
- 改善のコツ 欠品しやすい部品の出荷傾向を把握する
- 出荷量に見合った保管スペースを確保したい
- この状況どうする タイムリーな出荷体制が構築できない
- こうすれば改善できる 外部倉庫への大ロットの一括納品から、工場倉庫への複数回の直接納品に切り替える
- 改善のコツ 納品量を、標準化を念頭に適正化する
- 緊急出荷・特急出荷を減らしたい
- この状況どうする 臨時便や社用車での搬送が増えている
- こうすれば改善できる 庫内整理を徹底し、欠品の発生状況を可視化する!
- 改善のコツ 在庫制度の向上と欠品状況の見える化を徹底
- 非効率な庫内運送を解消したい
- この状況どうする 保管アイテムの取り違えが多発している
- こうすれば改善できる 適切な通路幅に修正して、庫内の作業導線を効率化
- 改善のコツ 庫内作業を行ううえで最適な通路幅を設定する
- 荷役作業で発生するムダを解消したい
- この状況どうする 荷繰り・荷探しが多くなってしまう
- こうすれば改善できる 固定ラックを導入して3定を実践、先入れ先出し法を励行!
- 改善のコツ 先入れ先出しがどうしたらできるかを工夫
- 作業スペースを十分に取りたい
- この状況どうする 狭いスペースなのに分担作業が多い
- こうすれば改善できる 出荷量や荷姿の見直し、作業台の高さ調整や工具置き場のレイアウト改善を実施
- 改善のコツ 出荷ロットを絞って荷姿を工夫する
- column 実在庫と在庫台帳の誤差
- 納期遵守と適正在庫のギャップを解消したい
- 第3章 物流ツールを使いこなして改善 パレットや段ボール箱の特性を把握
- 自動倉庫用のパレットの「たわみ」に対応したい
- この状況どうする パレットの荷崩れが出荷作業に影響
- こうすれば改善できる 平パレットに発生したオーバーハングを是正し、あわせて自動倉庫での過積載を回避する
- 改善のコツ 平パレットに合わせたバルク包装の導入
- 検品・梱包作業エリアのレイアウトを改善したい
- この状況どうする 出荷検品と梱包作業の連携が悪い
- こうすれば改善できる 検品作業台と梱包作業台の台車運搬をローラーコンベヤ搬送に切り替える
- 改善のコツ コンベア搬送を導入し、庫内搬送を効率化
- 積載率をなんとか向上させたい
- この状況どうする 出荷ロットが小さく、配送頻度が高い
- こうすれば改善できる 中継輸送やシェイクハンド輸送を導入し、積載率向上を推進
- 改善のコツ 荷室のすき間を可能な限り小さくする
- バラ積み貨物をまとめて積み込み時間を短縮したい
- この状況どうする 取扱量の変化に柔軟に対応したい
- こうすれば改善できる まずは「半量パレット積み」で積込み時間の短縮を図る
- 改善のコツ レンタルパレットの導入で手積み負担を軽減
- パレット上にきちんと段ボール箱を載せたい
- この状況どうする 段ボール箱の寸法がパレット積みに合わない
- こうすれば改善できる 段ボール箱、パレットの寸法を統一、適正化
- 改善のコツ パレットサイズから段ボール箱サイズを逆算
- パレット枚数の確認に時間がかかりすぎる
- この状況どうする 空パレットの管理を効率的に行いたい
- こうすれば改善できる 入出荷バースの壁面や支柱などに、目印となる空パレット枚数高表示をつける
- 改善のコツ 一目でわかる「現場の見える化」を実践
- 返却・廃棄パレットの扱いをきちんとしたい
- この状況どうする パレット返却置き場が乱雑で作業効率にも影響
- こうすれば改善できる 返却に際しての参考画像と注意書きを床面に張り付ける
- 改善のコツ 床面を活用して見本・手順などを共有
- column ハンディターミナルの導入
- 自動倉庫用のパレットの「たわみ」に対応したい
- 第4章 物流現場のしくみを改善 視点を変えて効率化を実現!
- フォークリフト荷役の作業負担を小さくしたい
- この状況どうする 空運行で稼働率が低い状態を改善したい
- こうすれば改善できる フォークリフトの台数を最小化し、空運行禁止を徹底し、かご車運搬も導入する
- 改善のコツ 庫内運搬機器の特性を念頭に適正化を実現
- 固定ラックを導入して平積みを減らしたい
- この状況どうする 出荷検品と梱包作業の連携が悪い
- こうすれば改善できる 固定ラックだけではなく、出荷頻度を念頭に移動ラックと仮設中二階を導入する
- 改善のコツ 出荷頻度に合わせたラック選択と保管エリアの効率的なレイアウトの設計
- 店舗納品にかかる荷卸し時間を短縮したい
- この状況どうする 手荷役を解消して効率化を図りたい
- こうすれば改善できる ハンドリフトの導入で納品プロセスを効率化
- 改善のコツ 搬入スペースに合わせた運搬機器を導入
- 小回りの利く物流センターを運営したい
- この状況どうする 出荷作業が特定のアイテムに集中している
- こうすれば改善できる バッファー倉庫を設けて特定アイテムの出荷に対応し、在庫量の標準化を実現する
- 改善のコツ 高頻度出荷品の独自のオペレーションを展開
- 冷蔵倉庫内の作業効率をもっと向上させたい
- この状況どうする 冷蔵倉庫内で作業時間が長くなっている
- こうすれば改善できる 出荷頻度別にロケーションを変更して、前面開口付近で迅速な出荷処理を行う
- 改善のコツ 保管と出荷の混在環境を改善
- 多頻度小口の出荷体制で同梱同送を徹底したい
- この状況どうする ヒューマンエラーが発生し、同梱漏れが続いている
- こうすれば改善できる 同梱同送のルールと同梱物のチェックリストを作成し、納品書一体型伝票を導入する
- 改善のコツ 納品書一体型伝票の導入で出荷作業を簡略化
- column 共同物流の導入
- フォークリフト荷役の作業負担を小さくしたい
- 第5章 物流コストをもう一度見直す ムダ、ムラ、ムリを繰り返しチェック
- タイムリーな納品体制を構築したい
- この状況どうする 入荷処理が遅れて入庫作業に手間取っている
- こうすれば改善できる 一度の発注量を抑えて、従来のバッチ納品を複数回に分割納品に切り替える
- 改善のコツ 倉庫内の物流波動を可能な限り解消
- 輸送コストを合理的な手法で削減したい
- この状況どうする 物流コストの上昇をなんとか抑えたい
- こうすれば改善できる 中継輸送による輸配送ネットワークの再構築に着手する
- 改善のコツ トラックドライバーの拘束時間を短縮
- 積載率を下げずにパレット荷役を導入したい
- この状況どうする 積込みに時間がっかり、荷役時間が長くなっている
- こうすれば改善できる シートパレットの導入でトレードオフを解消
- 改善のコツ 荷卸し、パレット積替えの作業負担を解消
- 館内搬送のしくみを変えて納品効率を改善したい
- この状況どうする 納品にかかる搬送時間を短縮したい
- こうすれば改善できる 納品トラックにダイヤグラム配送を導入し、施設内物流の一元化を行う
- 改善のコツ 共同一括納品に必要なデータを分析
- 非効率なパーツセンターのレイアウトを改善したい
- この状況どうする 誤出荷が頻発して作業効率が悪い
- こうすれば改善できる 顧客業態別グルーピングをした保管ロケーションに変更する
- 改善のコツ 保管効率より作業効率を重視したレイアウト
- column DPSの導入
- タイムリーな納品体制を構築したい
- 第6章 返品、リコール対応の現場改善 イレギュラーな物流管理に対応
- 返品商品管理と倉庫整理を効率的に行いたい
- この状況どうする 返品商品がどこにどれだけあるかわからない
- こうすれば改善できる 商品別に返品理由を確認したうえで、所番地化してある保管スペースに格納する
- 改善のコツ 返品処理のプロセスを明確化する
- 返品商品をしっかり整理・整頓したい
- この状況どうする 返品商品が似ていて区別しにくい
- こうすれば改善できる 実物大の写真を類似品の棚の間口に貼り付けて確認できるようにする
- 改善のコツ 高頻度の類似商品の画像一覧表も用意する
- 行き当たりばったりの都度回収を解消したい
- この状況どうする リコール製品の回収プロセスがバラバラ
- こうすれば改善できる リコール製品の修理業務を、工場から物流センターに移して一元管理する
- 改善のコツ 物流センター内に修理・交換本部を設置する
- リコール製品の部品交換後の返送工程を効率化したい
- この状況どうする 仮置きスペースが不足し、庫内作業に時間がかかる
- こうすれば改善できる 部品交換後の仮置き、運搬を工夫して効率化する
- 改善のコツ 修理ラインから出荷までの流れを簡略化
- 修理部品の在庫管理をしっかり行いたい
- この状況どうする 在庫適正化がなかなか実現できない
- こうすれば改善できる 生産ラインと保守・修理部門の在庫とロケーションは分けて管理する
- 改善のコツ 色別管理の導入で同一アイテム別用途を明示
- column 縦持ち荷役
- 返品商品管理と倉庫整理を効率的に行いたい
- 第7章 安全対策・火災対策の視点からの改善 作業負荷の小さな現場づくりを推進
- 庫内レイアウトの改善でフォークリフトの台数を最小化したい
- この状況どうする フォークリフトオペレーターが不足している
- こうすれば改善できる シャトル(搬送車)式の自動倉庫の動線とフォークリフトの動線を同期させる
- 改善のコツ フォークリフトの作業導線をこまかく分析
- 大型自然災害の発生に備えた倉庫整理を行いたい
- この状況どうする 雑然とした庫内外の環境を整備したい
- こうすれば改善できる 避難経路を確保し、荷崩れや荷崩落が発生しない庫内環境を構築
- 改善のコツ 倒壊などによる二次災害リスクを警戒する
- 合理的な台車運搬で腰の負担を軽減したい
- この状況どうする 非効率な運搬で腰の負担も大きい
- こうすれば改善できる 台車運搬の安全管理の基本ルールを定めて、腰痛防止策を周知徹底する
- 改善のコツ 運搬物の重量を可視化して作業負担を軽減
- ヒヤリハットを減らし配送時間を短縮したい
- この状況どうする より一層の安全・安心な配送ルートを構築したい
- こうすれば改善できる 配送エリア内のヒヤリハット発生地域を図示したエリアマップを作成
- 改善のコツ 安全性を確認しながら適正ルートを再構築
- 倉庫火災を発生させない庫内管理を実践したい
- この状況どうする 防災体制を充実させ万が一の火災に備えたい
- こうすれば改善できる 普通倉庫では現場レベルで危険物の指定数量をしっかり把握して十分注意して保管
- 改善のコツ 危険物や可燃物の大量の高密度保管を解消
- 倉庫業の火災保険
- 庫内レイアウトの改善でフォークリフトの台数を最小化したい
- 主要参考文献
- 索引
はじめに
物流コストの上昇も気になるので、なるべくお金をかけずに物流の現場改善を行いというニーズは大きくなっています。
大がかりなマテハン(物流関連)機器を導入した、情報システムの刷新を図ったりするわけでなく、まずは現場で創意工夫を凝らして物流改善を行いたいというわけです。
そのニーズに対応すべく、お金を使わずに頭を使って解決する現場改善の事例を集めて解説します。
欠品の多発を解消したい
在庫切れの状態
納期が迫っている部品の在庫がなく、納期まで余裕のある部品の在庫がある状況です。庫内のスペースはすぐに出荷する必要がない部品で占領され、急ぎの部品は欠品となっています。
また、納品実績が非常に少ない部品が余っていたり、すでに生産中止となっているモデルの部品在庫もかかえていることもあります。
出荷時期の迫る部品の保管スペースには、欠品の注意喚起の「赤札」を用意する
出荷量の少ない在庫は思い切って処分します。過去に納期遅れを発生させたことがる部品について、保管スペースに「赤札」を出し、欠品の注意喚起を徹底しましょう。
また。前期までの出荷実績、直近の動向を一覧表にまとめてグラフ化し、在庫量が不足しているようであれば、生産部門に確認するなどの体制をつくります。
固定ラックを導入して平積みを減らしたい
出荷検品と梱包作業がスムーズにいかない
庫内に平積みの品物があふれていたため、固定ラックを導入してこないを整理しました。当初こそ整理整頓が行き届いていたものの、出荷量が増えてきたため、再び平積みが通路に増えてしまったのです。
固定ラックの通路を利用したピンキング作業に時間がかかってしまい、平積み、仮置きの削減を図る必要があります。
固定ラックだけでなく、出荷頻度を念頭に移動ラックと仮設中二階を導入する
高頻度で出荷するものは固定ラックに置きます。あわせて中低頻度品を移動ラックに移し、効率的な出荷を可能にすることができます。
不動在庫(デッドストック)と低頻度出荷品は、出荷場所から一番遠くのラックに移し、固定ラックと出荷場所の近くにパレットステージ(仮設中二階)を設けることで、検品や流通加工をするスペースを確保しやすくなります。
トラックドライバーの拘束時間を短縮
輸送の起点、中継拠点、終点を結ぶネットワークにおいて、トラックドライバー当たりの担当輸送ルートを150~200kmを目安に区切り、中継拠点を設けます。日帰り距離を運行することで車中泊の発生などを回避して、拘束時間を短縮できるのです。
トラックドライバーの労働時間は細かく定義されています。原則1ヶ月284時間が上限(2024年4施行)です。
中継輸送の方法、トラックの運行ルート、荷役作業などについて標準的な段取りを決めておく必要があります。IT端末やスマートフォンを活用して、情報共有・案内通知など行い、トラックドライバーの乗り換え、トラクター交換、貨物の積替えなどで待ち時間が発生しない工夫も不可欠です。バラ積み貨物などは、待機時間が長くなるので、パレット荷役を設けてフォークリフト作業者を現場に配置しなければならない状況もあるでしょう。
台車運搬の腰痛防止策
ルール
●平坦な経路を通行
●過積載の回避
●前方確認できる積載高
●人力による押し運搬
●引っ張り運搬の禁止
●適切な速度での運搬(目安として4km/h以下)
●作業者の荷台搭乗を禁止
●走行中のストッパー禁止
●台車運搬中などに急激な姿勢変更や無理な姿勢を取らない
●人力運搬は1荷物25kg以内(それ以上は2人体制)
●長時間労度は避けて、規則的に小休止を取る
安全管理の視点から台車運搬の基本ルールを定めます。最大許容荷重や積載有効サイズを確認したうえで、積荷に重心が偏らないように荷物を載せてください。前方が見えなくなるまで載せるようなことは避け、人力で押して運搬し、ひっぱり運搬はしないでください。また回り道になっても平坦で十分な広さのある経路を通るようにしましょう。また、腰痛防止として、作業開始前に十分な柔軟体操をするとよいでしょう。
購入リンク
紙
※amazonの商品リンクです。画像をクリックしてください。